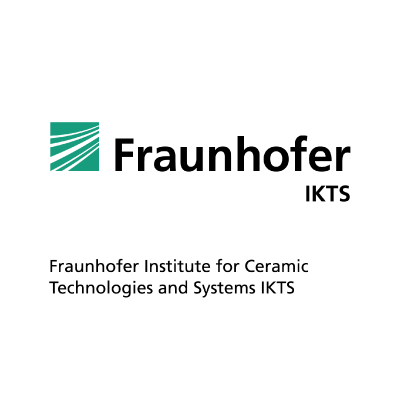
The Fraunhofer Institute for Ceramic Technologies and Systems IKTS is a research partner for the development of non-destructive testing methods, systems and devices. As a service provider and research cooperation partner, the institute provides its customers with competent support for the quality assurance of their products and manufacturing technologies in the fields of material and component diagnostics, condition monitoring, nanoanalytics and sensor technology as well as biotechnology and environmental technology. Current projects focus, for example, on quality assurance in lightweight construction, multi-scale material characterisation, life cycle management and reliability analysis, applied microelectronics including complex sensor systems with a special focus on assembly and interconnection technology. Fraunhofer IKTS continues to focus on the development and application of high-precision measurement and testing techniques for electronics, microsystems technology and nanotechnology, as well as the development and production of microelectronic components for measurement and testing procedures.
The department “condition monitoring and testing services” is made up of a multidisciplinary team from different disciplines (e.g. mechanical engineers, electrical engineering specialists, materials scientists and geophysicists). For more than 10 years, application-oriented solutions have been developed here for various industries (e.g. energy technology, process industry and transport). The entire value chain can be implemented here. Starting with specific simulations, possible measurement methods are selected and suitable measurement electronics are developed as well as data transmission and energy supply are ensured according to the requirements. Furthermore, IKTS has experiences in application specific design of electronics, sensors and circuits to guarantee a higher reliability.
Fraunhofer IKTS supports the project by developing the PZT data acquisition system (DAQ) and electronic components according to the specification for the wing application scenario. Simulations of the analog electronic components will be conducted and the embedded DAQ will be designed and realized by hardware in the loop development. The firmware for the data acquisition subsystem will be developed and continuously tested. A prototype of the SHM PZT-DAQ will be manufactured for the final demonstrator. The developed PZT DAQ will be integrated and deployed within the demonstrator components and test measurements will be conducted. Final optimization in DAQ firmware will be incorporated and the connectivity with the remote interface unit will implemented and tested.